The latest project has been a panel we have had on the to-do list for quite some time… The brake in our shop is JUST big enough to form this panel – it was one of the first things I checked when I got the brake home, because I knew we’d be making these sooner or later! It’s the vertical support section of the bonnet underpanel (also called the Lower Valance) – that houses the caged nuts for the bonnet hinges.
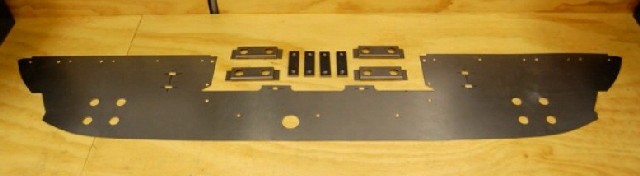
The first step is to carefully cut and punch the main piece from the pattern - one wrong hole and the whole piece goes in the recycling bin! Notice that the nut plates and cages are also formed up.
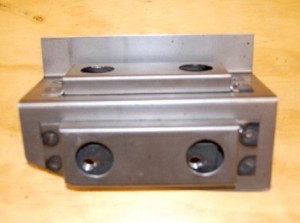
Next, the nut plates and cages are aligned and spot-welded to the backing plates. All of these pieces have the EXACT same dimensions as the original.
This is one of those panels that looks A LOT simpler than it turned out to be. I thought I would whip the prototype of this panel up in a few hours at the most. In the end, it took over 10… The final result, though, is a truly FABULOUS piece! I know the customer from Texas who ordered this will be very pleased, and thanks to their prodding, we’ve FINALLY gotten around to adding this panel to our available products.
This piece is GROUND ZERO for all bonnet alignment, and it needs to be correct and ROCK SOLID! You can save your underpanel (and over $1000!) by drilling this piece out of your current underpanel and carefully fitting in this new panel from Monocoque Metalworks. It is indentical in every dimension to the original, and now available in our online store!
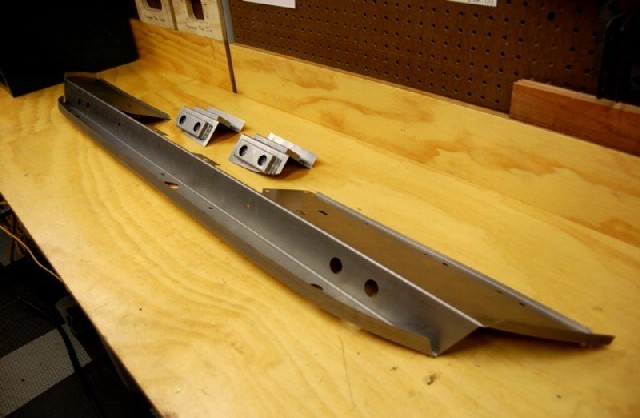
Here, the main panel has been folded on the brake, and the curved flanges have been formed on the bottom and sides - getting these formed properly without distorting the entire panel is no small task in itself! This is one of those panels that takes just about every machine in the shop to get right...
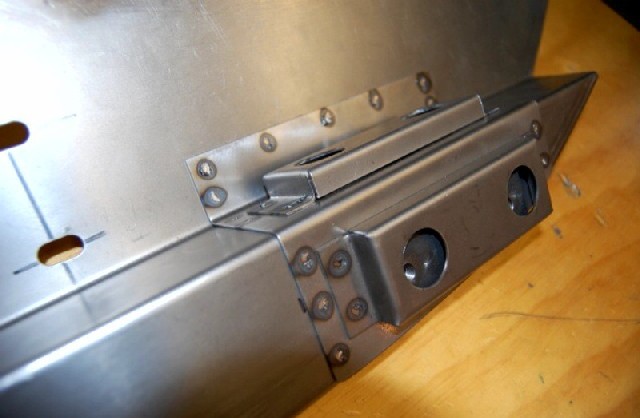
Now, the caged plate assemblies are spot-welded to the main panel. This is where things start to get hairy - if the panel fit and weld timer is not perfect, the spot-welder may "spit-out" a weld and erase hours of work!
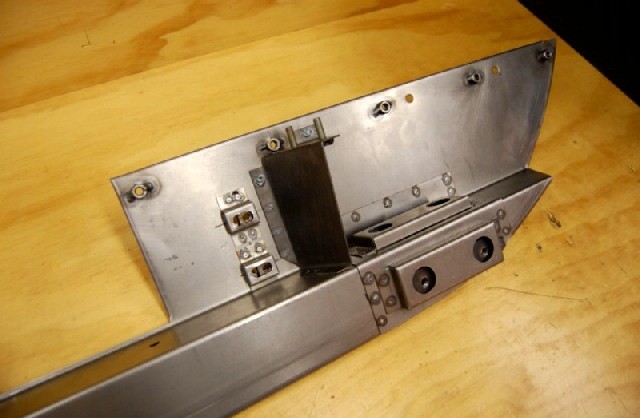
The horn bracket - which doubles as a reinforcing plate - is added, along with the caged nuts for the bonnet spring mounts, and welded nuts for the headlamp diaphragm mounting screws. We use 1/4-28 nuts here, and phillips-head machine screws to mount the headlamp diaphragm that exactly duplicate the original screws, but are much less likely to rattle loose over time.
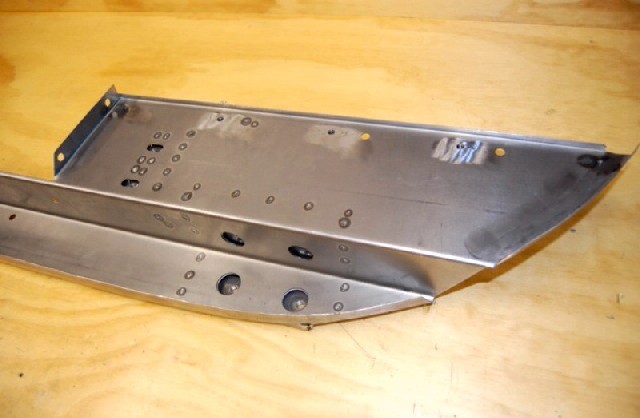
Here is a shot of the side that will be seen when the bonnet is assembled. Whenever possible, we attempt to pattern the spot-welds like the original - even though just going berserk with spot-welds would often be the most-accurate reproduction - the guys at Abbey Panels were a little crazy sometimes...
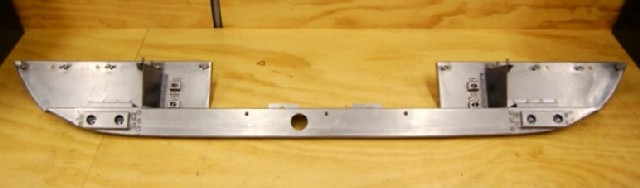
Finished! Wow - I can't help but be proud of this piece - I could have REALLY used this on my own car after "the BIG wreck" when I was 19 (not to be confused with any of "the smaller wrecks"...) This piece was cut, welded, hammered, and twisted back into the closest shape I could get to straight - which wasn't that close! Now, no-one has to go through that again! Whether this piece on your car is bent, or rusted, or BOTH - just drill yours out and weld in this new, perfect piece - available in our online store!